自上世纪70年代以来,六价格钝化膜的代替工艺就已存在。其中部分工艺是基于毒性较小的三价铬化合物,并且局限于性能低的亮蓝型涂膜,因而得不到广泛推广。由于这些替代镀液的配制价格相对低廉,而且这些镀液更换(倾倒)较频繁,因而维护/故障处理都不存在问题。
在过去几年里,业界对比六价铬工艺毒性更低的工艺的兴趣日益增加。部分原因是由于新颁布的废旧汽车(ELV)指令和废旧电子电器设备指( WEEE)令,这些指令要求在欧洲销售的汽车和电子零件不能再含有六价铬。
此外,人们正在寻找仅通过三价铬转镀膜就能达到的强化的性能特性。随着三价铬钝化工艺的发展,现在,我们已经能要求钝化膜必须提供较高的腐蚀保护性、耐热冲击性、染料和面涂吸收特性(同时保持外面的美观)以及成本有效性。也因此正确的配制、维护和故障处理技术变得极为重要。
以下介绍影响三价铬转镀膜性能的一些常见因素和一些鲜为人知的因素及故障处理方案。
内容概览:钝化时间、温度和浓度的影响;溶液搅拌;溶液的pH值;金属污染;镀层厚度;预浸镀溶液(出光液);水的质量;烘干温度。
常见的因素
01
三个[度“T”]
在金属精饰操作中最广为了解的三个因素被称为三个[度“T”]:时间长度、温度和浓度。
正像大多数工艺方案一样,必须将这些因素(变量)紧密地控制在具体的参数范围内,才能获得理想质量的表面。
02
时间长度
正确的沉浸时间是钝化工艺中最重要的一个变量。当镀锌工件沉浸在钝化溶液中,金属被溶解,并生成转镀膜。
溶液与电镀工件接触时间越长,发生转镀的机会也越多,而且在大多数情况中会导致较厚的钝化膜。
三价铬钝化液生成转镀膜的速度一般比六价铬钝化的慢。因此,对于一个厚膜转镀工艺需要60秒或以上的沉浸时间就一点也不奇怪了。这样,设备、过程周期等必须能够适应比过去更长的沉浸时间。
沉浸时间太短,会导致钝化膜厚度不够,因而使腐蚀保护性差。沉浸时间太长将导致过度消耗镀层,同样也使腐蚀保护性差。与六价铬不同,你通常不能通过简单的视察来确定转镀膜厚度。所以,操作工必须在过程中一直监控沉浸时间。
在工件一进入处理溶液时转镀膜就开始形成,而且直到工件进入第一个漂洗池时才停止形成转镀膜。
只要钝化液与被镀金属保持著接触,锌就持续溶解且转镀膜持续生成。当这个过程发生在实际的工艺池外面时,那么过程的进行就没有利用到热、搅拌以及工件界面上的正确的溶液转移。
因而生成质量差的转镀膜。为了尽可能减少这种情况,停留时间 特别是钝化池和第一个漂洗池之间,应保持尽可能短的停留时间。
03
温度
除了较长的沉浸时间外,高厚度/高性能的钝化膜通常在较高的温度下进行。在没有强矿物酸的情况下,这些类型的系统通常依赖热量来为转工艺的进行提供“热量”。因此,看到工作温度高达140-160℉也就很正常了。
在把温度考虑为一个可能的故障点时,重要的是对工件界面上的溶液而不是远离工件的溶液进行温度测定。
这种温度差异可能很大,特别是在大型工件刚入钝化溶液时。在某种情况中,在钝化前,工件要在一个漂洗池中预热。大多数情况下推荐使用聚四氟乙烯、特氟龙或石英浸入式电加热器。为了保证最佳的性能也建议使用自动温控器和溶液搅拌。
04
浓度
钝化液浓度是与旧的工艺差别很大的另一个因素,而且在排除故障时必须一直考虑这个因素。尽管六价铬钝化通常在1-5%体积浓度在运行,但高性能的三价铬钝化一般在10%或以上体积浓度下进行。
与温度的情况非常相似,需要这些较高的浓度来给镀液提供“能量”,生成理想的转镀膜。利用一个折射计可方便的测量池边浓度,而且应当通过湿分析或通过仪器进行确认
经常被问到“是否这三个因素之一可用于补偿另一个因素”。例如:较高的浓度是否能补偿沉浸时间太短?几乎在所有情况中,答案是否定的。
在时间长度、温度、浓度存在一个精确的平衡,这个平衡点可以使转镀膜在一个受控的速率下形成。如果工艺溶液的工作超出了制造商推荐的范围,那么几乎都会形成质量不良的转镀膜。
其他的因素
除这些“主要”的因素(变量)影响转镀膜工艺外,还有鲜为人知的其它工作参数,但却同样需要重要考虑。
01
搅动
溶液正确运动对于生成优质转镀膜是非常必要的。这可以通过空气、溶液(通过泵工作)或工件的运动来实现。不论采用哪种方法,重要的是在工件界面上具体合适的溶液交换。
在钝化过程中,发生许多化学变化。在有酸和三价铬错再得情况下锌很容易被氧化,结果导致在锌和钝化溶液街面上的pH值发生较大的升高。
这会引起氢氧化三铬在表面上析出,因而生成转镀膜。
如果没有正确的搅动,溶液很快就用尽了,因而不能生成足够的转镀膜。搅动的常用方法是利用一个低压鼓风机将空气迫入溶液。空气是从一个穿孔的管道(位于转镀池底附近)中泵出的,从而生产一个翻滚的运动。一定不要使用压缩机,因为它们不可避免地会使溶液受到灰尘及机油的污染。甚至使用一个鼓风机,也建议在进气管道上装一个过滤器。大量电镀的零部件,在钝化过程中通常会有足够的搅动,因而通常不需要空气。
02
pH值
pH值是工艺控制的一个重要方面,但常被忽视。厚膜三价铬钝化在非常窄的pH值窗口内进行,而且常常需要调整,不但在新配制时调整而且在正常工作过程中也需要调整。
如果实际工作的pH值超过推荐的工作范围,那么会阻碍转镀膜的形成,因而导致转镀膜太薄。pH值太低则会导致钝化膜快速地生成和剥离,同样形成的转镀膜厚度小,不能提供足够的盐雾保护。
可以利用仪表或者试纸来控制pH值。pH值在0-2.5范围时推荐使用非滤取型试纸。在正常工作条件下,钝化液的pH值将随时间而升高。可以向溶液中添加产品或稀释的硝酸来降低pH值。钝化溶液的pH值的下降是很少见的,一般是由于大量的拖带引起的。向溶液中添加稀释的苛性钠可提高pH值。推荐在钝化处理前使用体积比0. 5%至1%的硝酸预浸工件可提高镀锌的活性。
03
金属污染
金属污染的程度对钝化膜的性能可产生很大的影响。金属可能是通过工件的正常加工而被引入的(对于锌或铁),可能来自于外部源(例如紧固工件时所用的铜金属)或者可能是专利配方的一个组成部分(如钴)。不论金属污染的来源是什么,所有这些金属都会对钝化膜性能带来有害影响。
锌和铁是三价铬钝化中最常见的两种金属污染物。在这两种金属污染物中,铁污染的问题最大。
目前的技术趋向于比以前更加能容忍锌的溶解。经常能看到在锌浓度高于5000ppm的情况下钝化溶液仍能很好地工作。另一方面,铁对腐蚀性能产生很大的冲击,甚至是在铁浓度低至100ppm时。
由于钝化液配方本身具有酸性,因此溶液持续地与意外进入钝化液的工件发生反应。这就导致在钝化液中的积聚,最终会降低钝化液的寿命,增加了运作支出。为了避免这种情况,那些已从吊具上吊下来或从筐或桶中调出来的工件应被尽快取出。
钴是常被忽视的一种金属污染来源,因为它是作为专利配方的一个组成部分而被引入的。当钴金属以正确数量添加时,它起催化剂的作用,大大增加钝化膜厚度并提高腐蚀保护。如果钴和铬的比率太高,则钝化膜的形成受到阻碍,腐蚀保护性受到影响。
金属污染的程度过重的症状很难探查,但可以从钝化膜的变色或“混浊性”看出来。推荐对某些钝化液进行过滤,因为这有助于去除金属污染。也可以通过提高溶液浓度使金属污染的问题得到暂时为轻。还有一些专利添加剂,可用于将金属沉淀或抑制金属的溶解。
在某些情况中,过滤钝化液去除金属杂质,可有助于延长溶液的寿命。通常利用一个20-50微米的盘或筒式过滤器可完成过滤。推荐使用内衬聚丙烯的过滤泵。推荐每小时将溶液周转一次。
04
镀层厚度
一般来讲,对于一个优质的转镀涂覆需要锌的最小厚度为6微米。厚钝化膜可除去多达1-2微米的锌镀层。锌金属厚度小将导致FRR性能不良,在极端情况下会将电镀金属完全除去。在低电流密度区这种情况特别明显,因为在这些区域厚度趋向于达到最低。
05
酸预浸
在钝化前,表面不均匀或表面活性差都可能是影响转镀性能的因素。为了提供一个光亮、活性表面,通常先使用酸预浸工序然后紧接著进行转镀过程。当使用这个共序时,重要的是,要正确控制预浸液的化学组成,而且所用的酸要与钝化溶液兼容。
06
水的状态
钝化前和钝化后漂洗水的状态是一个很重要但常被忽略的变量。工艺池含有许多成分,如果它们被引入到钝化溶液中将是有害的。来自电镀池的锌金属、氯化物或氢氧化物,以及来自预浸工序的矿物酸,都将大大降低钝化液的寿命。
硬水盐也可以扮演金属污染物的角色,缩短钝化液的寿命。因此,应当将硬水软化或用去离子水、去矿物质水或反渗透水来替代硬水,然后才能将这些水用于制备钝化溶液。
钝化后的漂洗质量也是同样重要的。厚钝化膜通常具有较高的固体含量和表面张力,因而使漂洗水快速的被污染。随著漂洗液中浓度的增加,溶液开始越来越多地具有钝化液性质了。
结果是,在现有的转镀膜上又生成了质量差的转镀膜,这就大大减弱了总体性能。在解决任何钝化工艺故障时,要确信漂洗水的流速、搅动和沉浸时间都是足够用来提供足够的漂洗的。
07
烘干温度
当六价铬钝化膜受到高热时,它们通常在盐雾测试中表现不良。这是因为,六价铬系统一受到热就发生脱水并产生裂缝,因而露出下面的镀金属。所以白色锈蚀出现的相当快。试验显示,锌、锌-铁、锌-钴镀层上的六价铬钝化膜在接触到高温后将丧失多达90%的原始腐蚀保护。
耐热性是某些三价铬钝化膜的主要优点,但并不是所有系统都有这个优点。影响耐热能力的因素包括:水和作用的水平、是否存在面漆以及铬络合物的具体形式。测试显示,某些高性能三价铬系统在经受150℃的高温后,其腐蚀性能并没有恶化。然而,较长的烘干时间以及较高的烘干温度都会对性能产生不利影响。
08
处置
即使对工艺进行了最有力的控制,最终钝化溶液也会达到其寿命终点。而且必须废弃。不存在六价铬,就使处置工作变得更加简单,因为三价铬很容易作为氢氧化物被沉淀出来。
偶尔地,三价铬钝化溶液可能含有有机酸,有机酸会将某些金属络合。在这些情况中, 添加铁(以硫酸铁的形式)可便于金属沉淀出来。
典型废物处理循环操作可如下所示:
1.用水以1:1(1:更多)的比例稀释工作溶液。
2.添加0.5%硫酸铁(液体50%等级)。
3.给铁一定的时间使其在低pH值(1.0-2.0)下与钝化液发生反应。机械混合或空气搅动30分钟对这个过程有帮助。
4.利用液体苛性钠将溶液中和到pH值达到8.0-9.0,使用一个正确校准的pH仪表测量。 5.添加足够的聚合电解质絮凝剂,同时伴随轻微的混合。
6.发生絮凝和沉淀。
在采用任何废物处理的建议前,用户需要先了解当地/州/联邦有关现场或非现场的废物处理法规,因为这些法规可能要求获得处理废物的许可。如果有矛盾,要以这些法规为准。
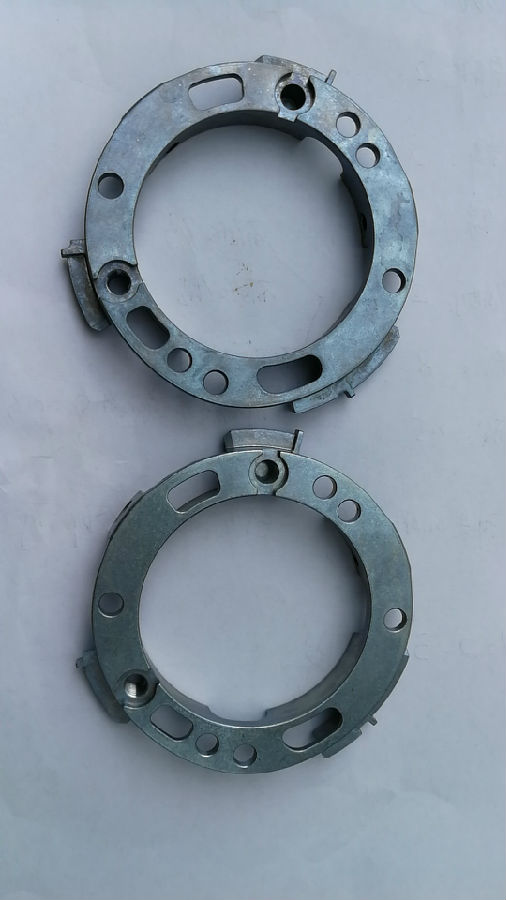
(铝合金本色钝化效果如图)
以上就是今天分享的内容,部分数据来源于网络,仅供参考,如有侵权请联系。