压铸铝切屑加工面与喷砂表面钝化后耐腐蚀性的哪种好
点击次数:390
发布时间:2025-05-09
压铸铝切屑加工面与喷砂表面钝化后耐腐蚀性对比分析
在压铸铝钝化工艺中,表面预处理方式(切屑加工面 vs. 喷砂表面)对钝化膜的质量和耐腐蚀性有显著影响。以下从微观结构、钝化膜完整性、腐蚀防护机制等维度进行专业对比:
1. 表面微观结构与钝化膜形成
指标 | 切屑加工面 | 喷砂表面 |
粗糙度(Ra) | 较高(Ra≈1.6-3.2μm) | 可控(Ra≈0.8-1.6μm,依砂粒调整) |
微观形貌 | 切削纹路、微裂纹、局部冷作硬化 | 均匀凹坑、封闭性表面,减少应力集中 |
污染物残留 | 易残留切削液、金属碎屑 | 砂粒残留风险(需酸洗或超声波清洗) |
切屑加工面缺陷:
切削过程中产生的微裂纹和毛刺可能成为腐蚀起始点,钝化液难以完全渗透,导致局部膜层不连续。
喷砂表面优势:
喷砂通过机械冲击封闭表面孔隙,形成均匀活化层,钝化膜覆盖更完整。
2. 钝化膜完整性对比
测试项目 | 切屑加工面 | 喷砂表面 |
膜厚均匀性 | 波动大(±0.2μm) | 均匀(±0.1μm) |
孔隙率 | 较高(>10 pores/cm²) | 较低(<5 pores/cm²) |
附着力 | 易在微裂纹处剥落(ASTM等级:3B) | 优异(ASTM等级:5B) |
腐蚀扩展机制:
切屑面钝化膜因表面缺陷易发生局部点蚀,腐蚀沿微裂纹快速蔓延。
喷砂表面钝化膜致密,腐蚀多为均匀缓慢扩展。
3. 耐腐蚀性核心数据对比
测试标准 | 切屑加工面(中性盐雾) | 喷砂表面(中性盐雾) |
首次白锈出现 | 48-72小时 | 96-120小时 |
红锈出现时间 | 120-168小时 | 240-360小时 |
腐蚀速率 | 0.05-0.08 g/(m²·h) | 0.02-0.04 g/(m²·h) |
加速腐蚀测试(CCT):
喷砂表面钝化件在30循环(湿热+盐雾)后仅边缘轻微腐蚀,切屑加工面则出现大面积鼓泡。
4. 机理解析
切屑加工面的劣势:
应力集中:切削导致的残余应力加速钝化膜开裂。
界面污染:残留切削液中的硫、氯离子破坏钝化膜钝态。
喷砂表面的优势:
活化效应:喷砂去除自然氧化层,暴露出新鲜铝基体,促进Cr³⁺均匀成膜。
机械键合增强:表面微坑增加机械互锁,提升膜层附着力。
5. 工艺优化建议
切屑加工面改进方向:
增加抛光或振动光饰,降低表面粗糙度(Ra<1.0μm);
强化前处理:电解脱脂+酸活化(如10% HNO₃浸渍30秒);
采用高浓度三价铬钝化液(pH 3.8-4.2),延长钝化时间至5-8分钟。
喷砂表面注意事项:
控制砂粒材质(推荐玻璃珠或陶瓷砂,避免Fe污染);
喷砂后24小时内完成钝化,防止自然氧化层再生;
优化钝化液流动性,确保深凹处覆盖(如增加槽液循环或超声波辅助)。
结论
喷砂表面钝化后的耐腐蚀性显著优于切屑加工面,主要归因于其更均匀的微观结构、更致密的钝化膜以及更低的界面污染风险。
高要求场景(如汽车、航空航天):强制采用喷砂+钝化组合工艺。
成本敏感场景:若必须使用切屑加工面,需通过抛光、强化前处理及延长钝化时间弥补缺陷,但仍需接受盐雾性能下降约30-50%。
实际生产中建议通过电化学阻抗谱(EIS)和扫描电镜(SEM)定期监控表面状态与膜层质量,动态优化工艺参数。
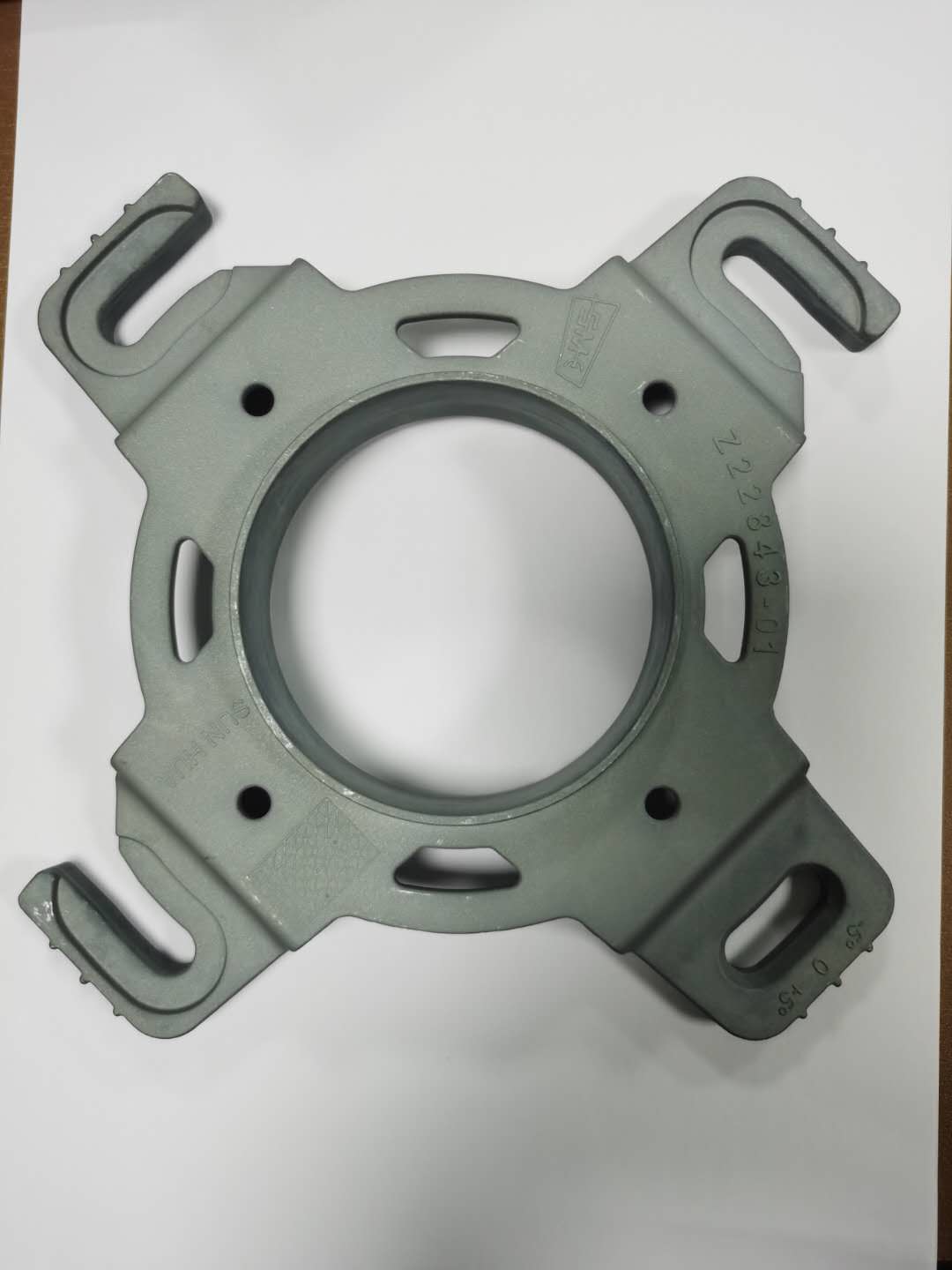